Comment numériser sa production au plus tôt pour en bénéficier rapidement?
Baisse des commandes, chaînes d’approvisionnement incertaines, guerres et conflits internationaux : les évolutions récentes ont mis de nombreuses entreprises en “mode réaction”, juge le Dr Christian Liedtke, manager de KUKA et CEO de l’Open Industry 4.0 Alliance.
Mais selon le Dr Liedtke, les planifications stratégiques ne devraient pas être repoussées plus longtemps. C’est justement maintenant qu’il faut se “relever les manches“, en particulier pour les entreprises industrielles de taille moyenne !(Source: Les PME ont-elles échoué dans l’industrie 4.0 ?)
La numérisation de la production met en lumière d’importants potentiels d’efficacité
Retrousser ses manches – cela vaut également pour une numérisation plus poussée de la production. Car le constat principal à l’ère de l’industrie 4.0 et de l’IIoT est le suivant : chaque entreprise est aujourd’hui une entreprise de logiciels.
Cela signifie que, dans l’industrie, la numérisation est une solution et qu’elle devrait être lancée et développée rapidement en tant qu’investissement stratégique pour l’avenir. Il est erroné de considérer la numérisation uniquement comme un projet informatique et un facteur de coûts.
Les potentiels de la production numérique sont importants : les processus et les chaînes d’approvisionnement sont organisés de manière nettement plus flexible, la productivité augmente et les coûts sont optimisés. Selon McKinsey, la production pilotée numériquement peut générer une énorme valeur ajoutée – par exemple, 30 à 50% d’arrêts machine en moins et 15 à 30% de productivité du travail en plus.
Selon McKinsey, une production pilotée par le numérique peut créer une énorme valeur ajoutée – par exemple une augmentation de 15 à 30 % de la productivité du travail ou une réduction de 30 à 50 % des arrêts de machines – Source: McKinsey – Link: http://tinyurl.com/2mqfumwj
Poser les fondations démarre par une connectivité complète dans l’usine
Les progrès toujours plus rapides de la numérisation s’accélèrent. “Nous allons assister à plus de changements technologiques au cours des 10 prochaines années qu’au cours des 50 dernières années”, a récemment déclaré le président américain Joe Biden en parlant de l’intelligence artificielle.
Mais en même temps, dans de nombreuses entreprises de taille moyenne, il manque encore une condition de base pour la transformation numérique et la fabrication intelligente : une connectivité complète au niveau de l’atelier, c’est-à-dire une connexion numérique des machines, des postes de travail manuel et des capteurs.
Même au cours de la troisième décennie de l’ère numérique, le grand défi des entreprises de fabrication reste la capture, l’harmonisation et l’utilisation de signaux provenant de machines et de sources hétérogènes dans des systèmes plus avancés.
Une connectivité complète fournit la base sur laquelle une plus grande productivité peut se développer :
- des processus et des chaînes d’approvisionnement optimisés
- Évaluations en temps réel sur le Topfloor et le Shopfloor (c.-à-d. dans les solutions ERP et MES)
- Intégration d’applications intelligentes telles que l’apprentissage automatique, la maintenance prédictive ou l’IA.
Chaque usine fonctionne avec un mélange individuel de machines, de postes de travail manuel et de capteurs, ainsi que d’autres sources telles que les données de l’usine. La base d’une représentation numérique complète des processus de production est la connexion numérique de toutes les sources de signaux et leur harmonisation dans un modèle de données sémantique – Photo: KamranAydinov auf Freepik
Parce que chaque usine est différente, la capacité d’intégration est essentielle
Dans l’industrie manufacturière, les objectifs sont les mêmes pour toutes les entreprises : durabilité, efficacité, productivité. Mais chaque usine fabrique ses propres produits, et les exigences sont différentes dans chaque usine. Chaque usine fonctionne avec son propre mix de machines, de postes de travail manuels, de capteurs, de solutions informatiques.
Le marché exige également une adaptation : les attentes des clients évoluent, les produits doivent être de plus en plus individualisés, les cycles de production se raccourcissent. “Par où commencer ?” se demandent certains directeurs de production. Le responsable informatique demande de son côté “s’il existe un outil informatique polyvalent pour la transformation numérique et l’usine intelligente ?”
Rester flexible grâce à la numérisation
La meilleure réponse à la complexité et au changement rapide est de rester flexible. Celui qui s’adapte le mieux survit. Pour la transformation numérique d’une production, cela signifie que les solutions informatiques intégratives et donc flexibles constituent aujourd’hui une colonne vertébrale solide.
- Solutions de connectivité pour une collecte et une harmonisation rapides des données – comme notre solution de collecte des données de production EGDGE CONNECT
- Solutions d’analyse pour des évaluations en temps réel – Comme nos solutions MES LITE, MES FLEX ou E-MES.
Exploiter le trésor du lac de données
À l’ère de la numérisation, les données du shopfloor sont pour l’industrie source de création de valeur – et plus précisément des informations préparées de manière sémantique à partir de machines, de capteurs, d’outils et d’entrées d‘opérateurs.
C’est pourquoi seule la connectivité au niveau du shopfloor permet d’accéder au véritable atout des entreprises industrielles, au trésor du lac de données. C’est là que la transformation numérique doit commencer.
L‘exemple de Siemens Energy : un onboarding pour 3.000 machines hétérogènes
Regardons l’exemple de Siemens Energy. Le leader mondial de la technologie énergétique a misé sur la technologie FORCAM pour la connexion numérique des machines de production sur 80 sites de production dans le monde. L’objectif du projet, prévu sur sept ans, est d’optimiser numériquement les processus de production sur 80 sites grâce à un système MES standardisé – par l’infrastructure SAP Digital Manufacturing (SAP DM).
Pour ce projet, FORCAM a fournit la solution FORCE EDGE CONNECT pour gérer l’Asset Onboarding jusqu’à 3.000 machines hétérogènes. Il s’agissait de collecter des données provenant des installations les plus diverses – presses, fraiseuses, poinçonneuses ou tours, ainsi que des machines avec ou sans commande logicielle propre.
La solution a réduit au minimum le travail de connexion pour les mêmes types de machines et a mis à disposition un modèle de données sémantique pour des analyses complètes dans SAP DM. Toutes les interfaces courantes étaient disponibles dès le départ (API/MQTT/OPC UA). Le déploiement a débuté dans cinq usines phares en Allemagne, en Grande-Bretagne et au Mexique. Un déploiement est prévu à l’échelle mondiale.
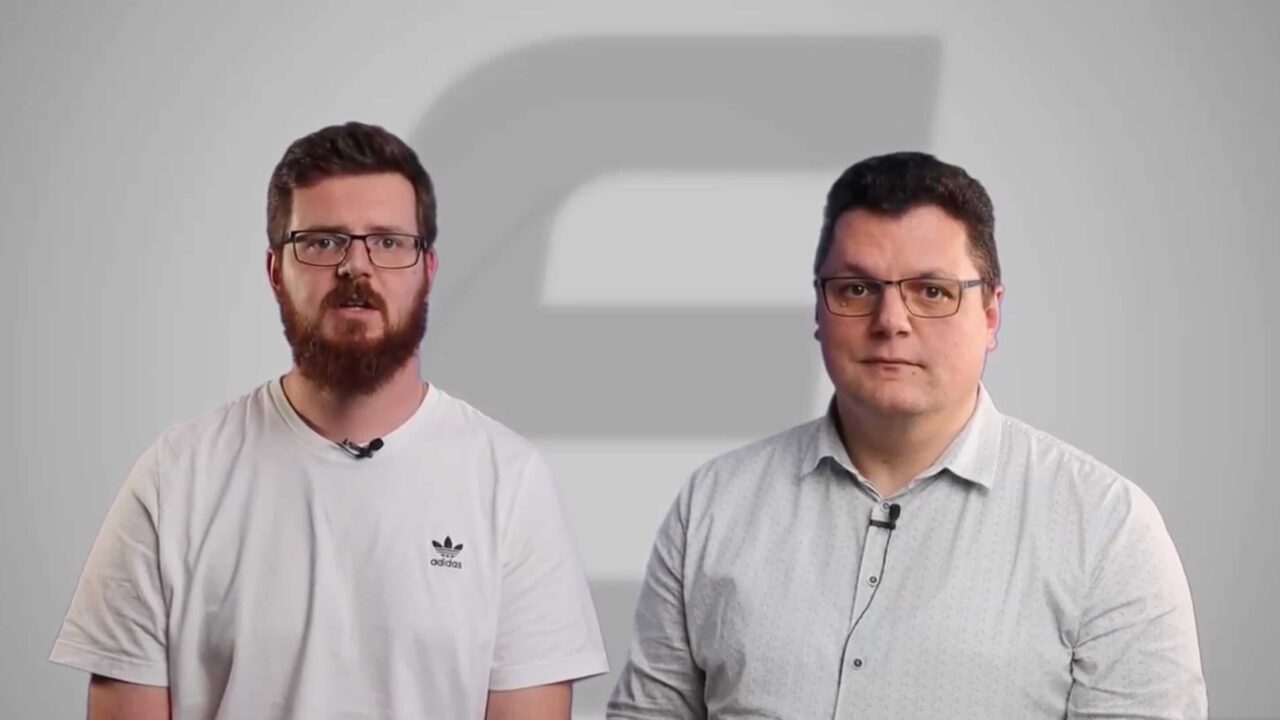
Les postes de travail manuels jouent un rôle important dans la fabrication à la commande et en série. La connexion numérique d’outils manuels comme une visseuse Atlas Copco grâce à la solution EDGE CONNECT de FORCAM est présentée dans la SAP Popup Factory à Walldorf – Photo: SAP
Postes de travail manuel – Démonstration dans l'”Industry 4.0 Popup Factory” de SAP
Outre les machines hétérogènes, la connexion numérique des postes de travail manuels est souvent considérée comme un défi particulier. Une station de démonstration dans l'”Industry 4.0 Popup Factory” de SAP à Walldorf montre à quoi ressemble une telle solution.
Dans cette usine de démonstration, des lignes de production pour la fabrication discrète et pour l’industrie de transformation sont installées. Les visiteurs sont les bienvenus pour découvrir la valeur ajoutée des solutions SAP dans un environnement réaliste de shopfloor.
La démonstration pour les postes de travail manuels démontre de manière exemplaire le montage d’un composant électronique : Sur un poste de travail manuel, une personne utilise une visseuse de précision. Les pièces nécessaires sont amenées par un bras robotisé sur lequel est installée une caméra.
La visseuse et la caméra du robot sont reliées par FORCE EDGE CONNECT. La solution FORCAM génère un modèle de données à partir des signaux et le met à disposition de SAP Digital Manufacturing pour l’inspection virtuelle conviviale du montage.
Profiter de la numérisation avec un logiciel MES
Cycles de vie des produits plus courts et plus de variantes : Les entreprises doivent répondre à ce changement de paradigme dans la production par la transparence et la flexibilité. Ces deux objectifs d’efficacité ne peuvent toutefois plus être atteints aujourd’hui par la seule transformation physique des lignes de production. Il est nécessaire de miser sur des logiciels permettant d’atteindre une transparence et une efficacité accrues.
La solution à l’ère de la numérisation et de l’automatisation est la suivante : les méthodes du lean management doivent être soutenues par un logiciel d’usine moderne – un Manufacturing Execution System (MES). Objectif de ces outils : plus d’efficacité et moins de gaspillage.
Le logiciel d’abord : Une plus grande transparence et une plus grande flexibilité sont aujourd’hui obtenues grâce aux MES. Les MES permettent de réduire les coûts grâce à des outils tels que la surveillance de l’énergie et l’analyse des performances. Les équipes formées sur un MES performant peuvent réduire les coûts d’énergie et de ressources de plusieurs dizaines de pour cent sur une seule année. La flexibilité rend les chaînes d’approvisionnement plus résilientes. Pour le dire simplement : Si le fournisseur A tombe en panne, la production doit pouvoir se tourner rapidement vers le fournisseur B. C’est ce que permet un MES.
Un flux de données continu et en temps réel – de l’usine aux finances – est l’objectif d’une numérisation réussie des processus au niveau de l’atelier et de la surface de travail.
Conclusion : la nécessité de la numérisation n’a jamais été aussi grande
La nécessité pour les entreprises d’organiser leur production de manière numérique n’a jamais été aussi grande. Les entreprises devraient planifier la transformation numérique par étapes. Si elles veulent être plus efficaces, plus résilientes et plus durables, elles doivent placer la connectivité des machines et la sémantique des données correspondantes en tête de leur stratégie.
- La première étape : poser les fondations. Ce n’est que lorsque les machines hétérogènes, les postes de travail manuel et les capteurs sont connectés numériquement que les avantages de la Smart Factory peuvent être pleinement exploités.
- L‘étape suivante : la connexion aux solutions MES et ERP peut suivre, afin que les systèmes puissent réellement travailler avec de véritables données de production en temps réel.
Le plus important pour la transformation numérique sont le courage et la rapidité.Nous connaissons depuis 15 ans les possibilités offertes par Internet dans l’industrie. Il faut maintenant les exploiter.