Heterogene Maschinenparks einfach digital anbinden – Folge 2: Montagelinie
Industrie 4.0-Prozesse durchlaufen mehrere Phasen: Connectivity, Visibility, Transparency, Predictions, Adaptability bis hin zu digitalen Services, die die Prozesswelt der Produktion ergänzen. Insbesondere für Anlagen aus dem Brownfield, also dem vorhandenen Maschinenpark, gilt: Das Herzstück ist die Connectivity. Sie muss von Anfang an in eine ganzheitliche OT/IT-Architektur eingebunden sein. FORCAM und SAP bieten diese ganzheitliche Architektur in der SAP Digital Manufacturing Cloud an.
In sechs Beiträgen für gängige Maschinentypen skizzieren wir, wie Unternehmen mit dem Connectivity-Layer FORCE EDGE CONNECT alle Maschinen – unabhängig von Herstellern, Jahrgängen und Steuerungen – anbinden und die Daten beispielsweise in der SAP DM (Digital Manufacturing) oder SAP ME/MII weiterverarbeiten können.
Folge 2: Montagelinie
Montagelinien in Fabriken stellen sehr komplexe Abläufe dar – von der Rohstoff- und Teile-Anlieferungen über die eigentliche Montage bis zu Maler- und Lackierarbeiten, Lagerung und Auslieferung. Entsprechend existiert eine große Variantenvielfalt unterschiedlicher Montagelinien. Daher benötigt das Einrichtung und Betreiben einer Montagelinie eine ausgeklügelte Planung von Workflows und Logistik. Eine cloudbasierte, digital gesteuerte Fertigung (Data-driven Manufacturing) bietet dabei größte Vorteile.
Zur Vereinfachung gehen wir in dem folgenden Beispiel einer Montagelinie davon aus, dass es sich um die direkte Verbindung von manuellen Montagelinien handelt, die logisch aufeinander aufbauen.
Daten erfassen
Grundsätzlich ist bei der Gestaltung von Montagelinien darauf zu achten, wo Daten abgegriffen werden sollen. Es gibt die Möglichkeit, die Daten
- an jedem einzelnen Montageschritt über eine entsprechende Arbeitsplatzsteuerung zu sammeln
oder
- die gesammelten Informationen erst am Ende der Montage über eine Kopfsteuerung zu erfassen.
Die Datenerfassung über eine Kopfsteuerung ist in diesem Fall deutlich einfacher in der Gesamtumsetzung als die Erfassung an jedem einzelnen Arbeitsplatz.
Manueller Montagearbeitsplatz
Beim manuellen Montagearbeitsplatz muss bei der Planung der Soll-Architektur unter anderem darauf geachtet werden, welches die relevanten “Quality-Gates” im Montageprozess sind und wie diese Informationen in die Gesamtbeurteilung des Arbeitsergebnisses einfließen sollen. Zudem fließt die Auswahl der geeigneten Plug-Ins zur Kommunikation mit den einzelnen Steuerungen der Arbeitsplätze in die Soll-Architektur ein.
Dabei senden die Steuerungen der Arbeitsplätze beziehungsweise die Kopfsteuerung der Linie Daten über die Plug-Ins an das Edge-Modul „FORCE EDGE CONNECT Machine Connectivity and Model“. Dort werden die empfangenen Daten in einem semantischen Datenmodell zusammengeführt, das heißt, jedes Signal erhält seine spezielle Bedeutung. Diese semantisch aufbereiteten Informationen werden anschließend über standardisierte Maschinenevents an ein übergeordnetes Drittsystem übertragen, beispielsweise die SAP DMC (Digital Manufacturing Cloud) oder SAP ME/MII.
Autor: Marc Fröschl (Head of Product Management)
Serie: Heterogene Maschinenparks einfach digital anbinden
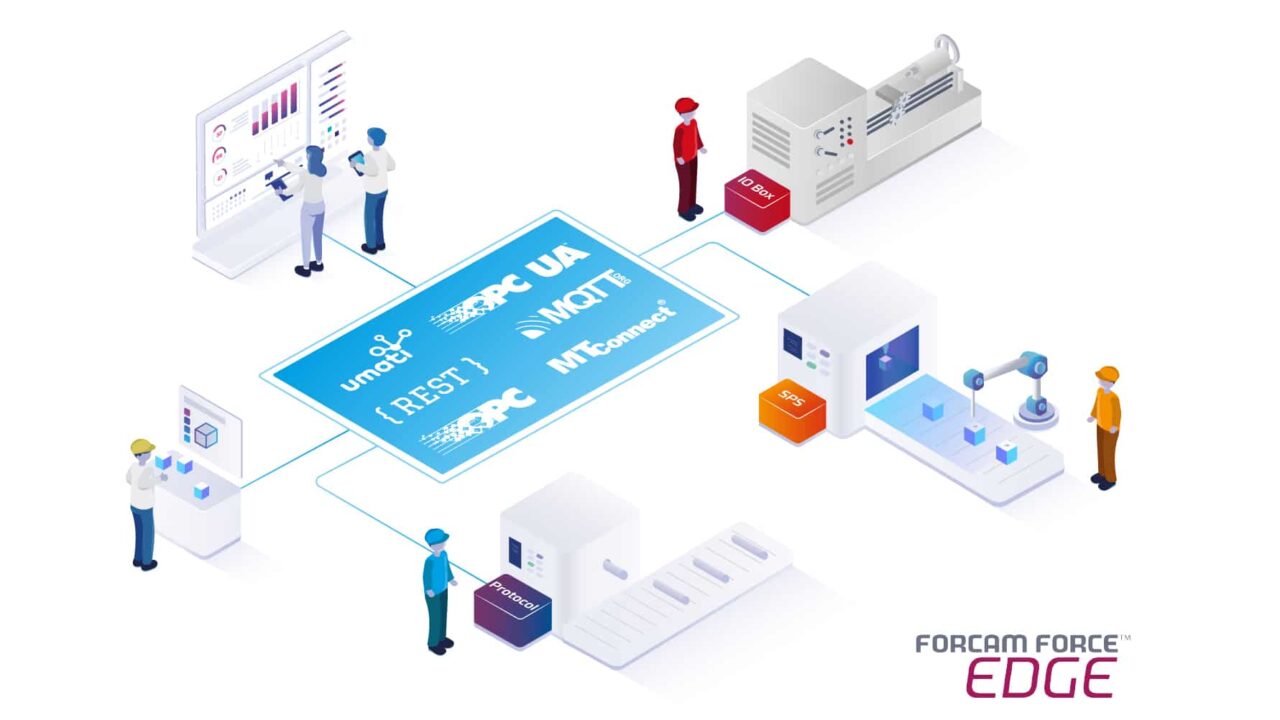
Über den Autor
Oliver Hoffmann ist Geschäftsführer bei FORCAM, zuständig für den weltweiten Vertrieb, das Marketing, das Partnergeschäft sowie die Digitalisierung ausgewählter Geschäftsprozesse. Der studierte Wirtschaftsinformatiker hat über 25 Jahre Erfahrung im Vertrieb von beratungsintensiven Software-Lösungen.