Three steps to smart manufacturing with the cloud: Connect machines, record signals, evaluate data
Good news: German industry’s order backlog reached a new high this February (range of the order backlog: 7.1 months) – a report that tends to go unnoticed in times of pandemics and elections.
At the same time, the smart factory is becoming the new normal. “There is massive digitalization in industry,” Gunther Kegel, new president of the German Electrical and Electronic Manufacturers’ Association (ZVEI), told the Frankfurter Allgemeine Zeitung. “Times of such great change always also means the opportunity for economic prosperity,” Kegel said.
Economic opportunities and digital transformation are closely related. To remain competitive, small and medium-sized enterprises (SMEs) in particular need quick-to-implement and straightforward solutions for future-proof manufacturing. This is precisely the approach taken by the SaaS concept (“Software as a Service”) – to increase the efficiency of the entire company simply, quickly, and cost-effectively.
Added value through digitalization
Digitalization is not an end; it must create measurable added value through higher efficiency and competitiveness. It is about innovative products, better production, higher delivery reliability – and all this at manageable and predictable costs.
These primary strategic goals can be realized easily and quickly with a standardized complete solution à la SaaS. With SaaS, SMEs can start their digital transformation without building up new IT resources of their own. Results are transparency in production, followed by higher efficiency and productivity.
Step 1: Connect machines
Digitalization only exists with connectivity. First of all, the signals from the machines must be recorded. The signals are processed into data and sent to the software in the cloud. From there, they are returned to the screens of the factory teams in real-time as user-friendly analyses. This ensures the most excellent possible transparency and higher efficiency.
The basic structure of the MES LITE solution is designed to be “ready to run” and enables companies to connect and roll out the solution in production independently. The first step – the machine connection – is pre-configured in the solution. The software is available in the network, and the required hardware is supplied:
- FORCAM I/O controller for a machine connected to the Ethernet network as well as
- the central signal processing and interface to the cloud, the Edge Gateway.
Additional machines can be connected at any time.
Step 2: Acquire machine data
Machine data acquisition (MDC) in the standardized MES LITE solution provides data and information on the current status of a machine or a plant. In this way, developments and trends can be analyzed in a differentiated manner, and different workplaces can be compared.
The MDE is carried out by two function modules: the Data Collection Unit (DCU) and the Data Acquisition (DACQ). Both modules run on the central hardware interface between production and the cloud – the Edge Gateway. The basic configurations of the modules for the FORCAM I/O Controller connection type are supplied.
As standard, four signals are digitally recorded from the customer’s machines/plants, or less if desired: Machine switched on; Automatic ON/OFF; Machine producing; Machine stopped.
The following operating states are derived from the acquired signals:
- Machine running (production)
- Machine not running (standstill) with the reason (cause)
- No connection (operating status unknown/no network connection)
The worker at the device can thus qualify unjustified downtimes by the actual reason. Forepersons or supervisors can also make corrections.
Step 3: Objective real-time analyses enable ongoing optimization
In the MES LITE solution, the software in the cloud visualizes all operating states precisely in real-time on the shop floor terminal in the factory. The shop floor terminal is a web interface for the browser-enabled end devices on the machine.
Added value through digital machine data collection:
- The temporal availability of a machine / plant is displayed objectively and transparently. Based on the machine availability, downtimes and maintenance times can be determined and optimized.
- The current operating status of all machines or systems can be seen. The frequency and duration of the various operational states and their causes provide essential information for optimizing production and maintenance.
An objective calculation of hourly machine rates becomes possible because all information is accurate.
Author: Maurice Fackel, Business Development Manager bei FORCAM
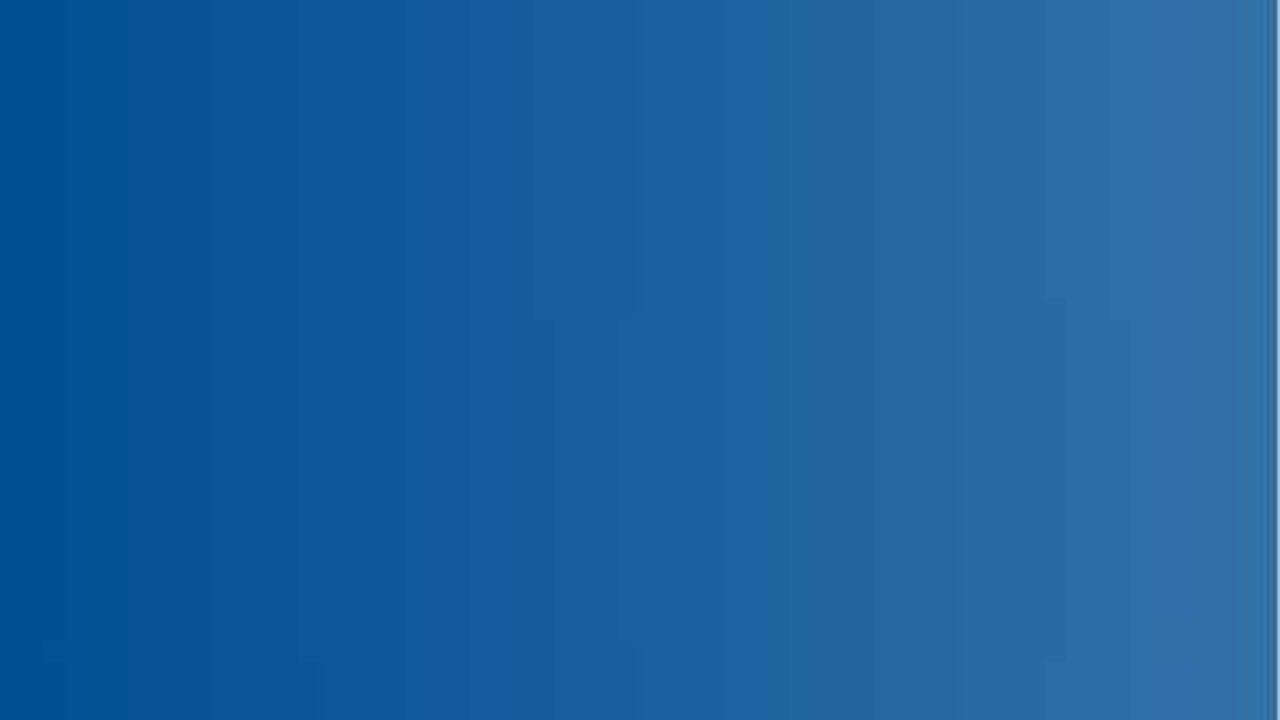
Your contact person
Do you want to know more about this topic? As your contact person, I will be happy to answer any open questions you may have about our solutions. You can reach me at: Siegfried.Maigler@forcam.com